Warehousing and storage

Warehouse
This page provides occupational health and safety guidance for the storage and warehousing sector.
This page will help employers understand:
- which topics are the main causes of injury and ill health in storage and warehousing;
- where to get useful guidance on how to manage these risks;
- how to manage health and safety in warehouses to ensure compliance with legal requirements.
Ten safety essentials
Take a look at our ten safety essentials pages. These pages will guide you through the essentials for managing health and safety in your business. The areas below contain specialist advice for you to consider when writing your risk assessments and implementing safe systems of work & procedures to keep staff and visitors safe.
Risk assessment
When undertaking your risk assessment for your business you may wish to look at these examples to give you ideas of hazards and control measures:
- Example risk assessment for a warehouse (PDF, 267KB)
- Example risk assessment for a cold storage warehouse (PDF, 194KB)
Many warehouse facilities also have offices, so you may wish to look at our Office based businesses guidance
Slips & trips
What you must do
You must ensure that your employees and anyone else who could be affected by your work (such as visitors and members of the public), are kept safe from harm. You must assess the risk from slips and trips and take reasonable precautions.
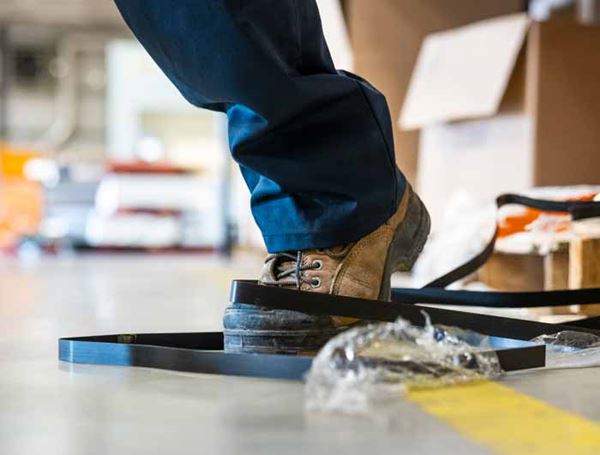
What you should know
Slips and trips remain the single most common cause of major injury in the retail sector. Most accidents occur when
- smooth cleaned floors are left wet;
- spills are not cleaned up quickly and effectively; and
- when there is failure to keep the floor free from contamination.
For more information see the links below;
Electrical safety
Electricity can kill or severely injure people and cause damage to property. However, employers can take simple precautions when working with or near electricity and electrical equipment to significantly reduce the risk of injury to you, your workers and others around you.
In order to comply with the law you should:
- Ensure the electrical installation is inspected and maintained in good repair; and
- Ensure that any portable appliances are inspected and tested regularly (PAT Test);
- Keep a records of inspections and tests.
See our Electrical safety page for comprehensive guidance.
Electric Vehicles
Lift trucks
Forklifts are incredibly useful pieces of equipment, used throughout many industries to enhance productivity, speed up processes and protect the health and safety of employees. But they can also be extremely dangerous, with thousands of forklift accidents every year resulting in sometimes serious injuries, and usually caused by improper and unsafe operation or lack of training for the operatives.
- Lift trucks are particularly dangerous in the workplace.
- On average, lift trucks are involved in about a quarter of all workplace transport accidents.
- Accidents involving lift trucks are often due to poor supervision and a lack of training.
Training
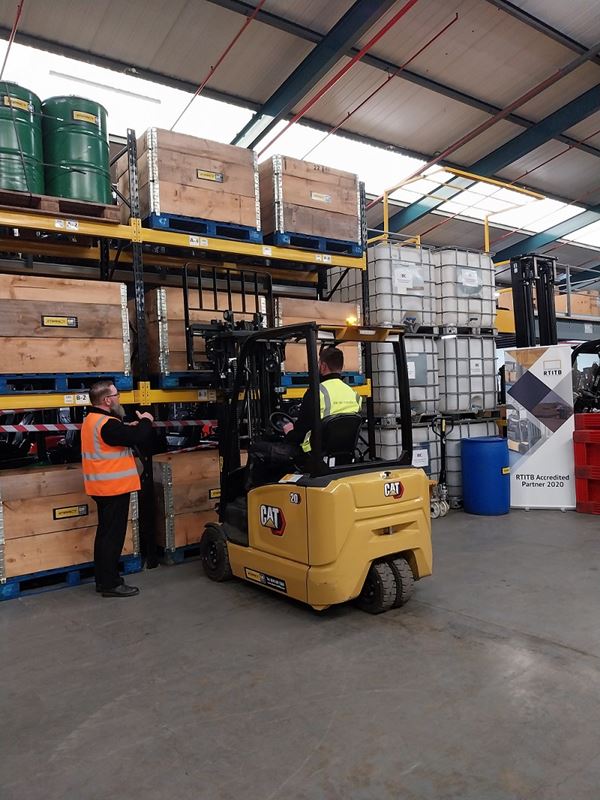
HSE has published an Approved Code of Practice (ACOP) and guidance called Rider-operated lift trucks: Operator training and safe use. Approved Code of Practice and guidance.
This sets the minimum standard of basic training people should receive before they are allowed to operate certain types of lift truck - even if they only operate the equipment occasionally. It also provides detailed guidance about how they can meet this standard.
The ACOP covers stacking rider-operated lift trucks, including articulated steering trucks. 'Rider-operated' means any truck that can carry an operator and includes trucks controlled from both seated and stand-on positions.
If you employ anyone to operate a lift truck covered by the ACOP, you should make sure that operators have been trained to the standards it sets out. Also see Lift truck training - guidance for employers (HSE)
- FS01 – What is the minimum age for operating fork lift trucks?
- FS02 – How long does a fork truck driver’s licence last?
- FS06 – Fork lift truck operator training – recognised accrediting bodies
- FS09 – Training requirements for hand pallet trucks
- FS12 – The Legal Requirements for Fork Lift Truck Operator Refresher Training
- FS16 – Overseas Fork Lift Truck Operator Licences
- FS19 – Medical Standards for Fork Lift Truck Operators
- FS23 – Fork lift truck operator training
- FS30 – Operator training for forklift truck engineers and sales personnel
Service
Lift trucks are work equipment and as such must be inspected and maintained to prevent them becoming a danger. Lift trucks need to be served as well as having their Thorough Examination. They are both important but distinctly separate .
- FS10 – Fork lift truck maintenance is a legal requirement
- FS20 – Fork lift truck tyre safety
- FS21 – Cleaning a fork lift truck
- FS28 – Fork Lift Truck Operator Daily Checks
- FS22 – Fumes associated with fork lift truck operations
- FS32 – Welding fumes
Thorough Examination
Thorough examination of industrial lift trucks is required under health and safety law: LOLER 1998, which covers lifting equipment, and PUWER 1998, which deals with all other safety-related items, such as brakes, steering and tyres. Your regular inspections as part of a preventive maintenance scheme or scheduled service are not a thorough examination. INDG422 Thorough examination of lifting equipment (PDF) . If you lift truck only lifts good, then you must have an annual check. If you lift persons then the check must be every 6 months.
- FS03 – Is Thorough Examination of a fork lift truck a legal requirement and what is it?
- FS04 – Does a Thorough Examination Cover the Requirements of Both LOLER and PUWER?
- FS17 – How long does a Thorough Examination last?
Daily checks
Whatever you call them on your site, pre-use, pre-shift or daily checks they form an important part of most companies’ Safe Systems of Work. Daily checks are crucial to ensuring fork lift trucks are in safe working order; providing a regular opportunity to identify any issues before they lead to more serious and costly problems.
Further information on pre-use checks: RTITB and Fork Lift Truck Association
Further information;
- Use lift trucks safely (HSE)
- Working platforms (non-integrated) on forklift trucks (HSE)
- Using a Lift Truck on or near a road
- FS05 – What is the maximum gradient for a fork lift truck?
- FS07 – Fork lift trucks and the use of mobile phones
- FS11 – Load rating of fork lift trucks
- FS13 – Safe Storage of Liquefied Petroleum Gas (LPG) Cylinders
- FS14 – Rope Evacuation From Mechanical Handling Equipment
- FS18 – The Use of Working Platforms on Fork Lift Trucks
- FS24 – Supervision of fork lift truck operations
- FS25 – Speed and fork lift trucks
- FS26 – Towing with a fork lift truck
- FS27 – Pallets
Work at height
Any work at height, including maintenance work undertaken for you by a contractor, must be properly planned, appropriately supervised and carried out in a safe way. Avoid work at height if you can, but if it cannot be avoided, select the correct equipment for the task. People can fall from stepladders or ladders.
- Where they are used you must be able to show that it is not reasonably practicable to select alternative, safer equipment because the task is low risk and short duration.
Mezzanine safety gate prevents accidental falls - Never use pallets on fork-lift trucks for accessing work at height or as working platforms.
- Never climb on racking unless it is specifically designed for use as access equipment.
- Make sure that everyone involved in working at height has the ability to do the work safely, training may be needed.
- Some access equipment may require specialist training, e.g. a mobile elevating work platform (MEWP).
- Inspect equipment used for work at height (such as ladders) to make sure it is safe. Do this before use, periodically and after an incident that might affect the equipment’s safety.
- Ensure that open edges of mezzanine floors are suitably guarded, with gates to access them.
- Loading bay edges should be clearly marked, or where appropriate guarded, with gates for access during loading/unloading.
Storage systems, including racking
Storage areas should be properly designated and clearly marked. The layout of storage and handling areas should avoid tight corners, awkwardly placed doors, pillars, uneven surfaces and changes of gradient.
Pallets
Inspect pallets each time before use to make sure that they are in a safe condition. Take damaged pallets out of use for repair or destruction. Handle empty pallets carefully – do not drag or throw them about. Pallets should be loaded correctly to ensure load stability; banding, shrink or stretch wrap can help with this. If you use pallet racking in your warehouse, make sure the pallets you use are suitable for the type of racking you have.
See Safety in the use of Pallets PM15 & FS27 – Pallets
Racking systems
Racking systems should be properly designed and installed, this includes being able to safely take the load of the goods being stored. Protect racking if it is likely to be struck by lift trucks and other vehicles. Inspect racking regularly to make sure it is repaired and maintained properly and is safe. You should use three types of inspection:
- immediate reporting of damage and defects;
- visual inspections at regular intervals; and
- ‘expert’ inspections carried out at intervals by a competent person e.g. SEMA approved rack inspectors
Where you find damage that affects the safety of the racking system, offload the racking and introduce controls to prevent it being used until remedial work has been carried out. Keep a record of inspections, damage and repairs, e.g. in a logbook.
Persons undertaking the regular inspections of their companies racking should have suitable knowledge and training, for example have attended a training course such as the SEMA rack safety course
You should display load notices on your racking; SEMA load notices
For more information see
Manual handling
What you must do
The Manual Handling Operations Regulations 1992 (MHOR) require employers to:
- avoid the need for hazardous manual handling, so far as is reasonably practicable;
- assess the risk of injury from any hazardous manual handling that can't be avoided; and
- reduce the risk of injury from hazardous manual handling, so far as is reasonably practicable.
Your risk assessment should cover all standard operations, including cleaning and maintenance activities. It should reflect how the work is actually done.
The main areas you should focus on are the task, load, working environment and individual capability.
What you should know
Back pain and other aches arising from manual handling injuries are the most common type of occupational ill health in the UK. Lifting and moving by hand is the main cause of reportable accidents in the 'freight by road' industry. There were 278 major and 3639 over-3-day injuries reported in 2006/07 work year. Bad backs were the most common injury.
- Use the free HSE Manual Handling Assessment Chart (MAC) , to identify the tasks which present the greatest risk.
- Ask employees about what they consider to be the most hazardous lifting and moving jobs.
- Consider whether high hazard manual lifting and moving jobs can be avoided, for example by palletising heavy or bulky products.
- Consider whether a load can be changed to make it easier to carry, for example, smaller packages, providing handles or hand-holds.
- Consider the use of mechanical aids, such as vehicle mounted hydraulic hoists, portable roller conveyors, pallet trucks, scissor lifts and customised trolleys. These can save a lot of time and money, as well as saving backs.
- Roll cages are commonly involved in manual handling injuries. Ensure roll cages are sensibly loaded, properly secured in the vehicle and that pavement access at the delivery end is relatively level and free from potholes and obstructions.
Further information:
- INDG398 - Are you making the best use of lifting and handling aids? (PDF)
- Research on furniture distribution (PDF) - Useful for many other types of distribution.
- Manual Hanlding Assessment Charts (MAC)
- Manual handling at work: A brief guide
- Managing upper limb disorders in the workplace
- Manual handling assessment charts (the MAC tool)
- Risk assessment of pushing and pulling (RAPP) tool
- Assessment of repetitive tasks of the upper limbs (the ART tool)
- Roll cages and wheeled racks
Mechanical handling
Mechanical handling equipment (e.g. a fork-lift truck) should be suitable for the job it is used for. All industrial truck operating areas should be suitably designed and properly maintained. Industrial
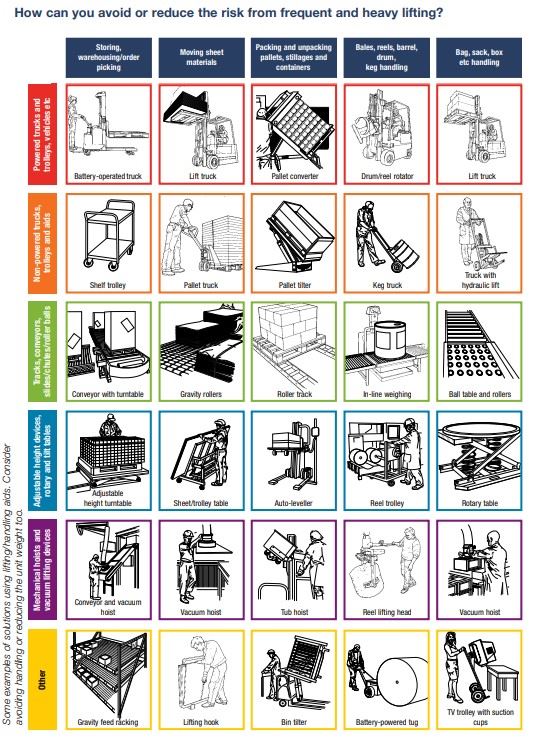
truck operators need to be trained by a competent person. Operator training should include the following three stages:
- basic training;
- specific job training; and
- familiarisation training
Further information;
Workplace transport
Moving vehicles need to be carefully managed to control and reduce the likelihood of accidents.
Consider and put in place control measures for:
- Managing deliveries and visitors
- Pedestrian safety
- Traffic routes
- Reversing vehicles
- Coupling and uncoupling
- Load safety
- ‘Driveaways’ or premature vehicle departures
For more information see:
Loading and unloading
Loading and unloading can be dangerous. Machinery can seriously hurt people. Heavy loads, moving or overturning vehicles and working at height can all lead to injuries or death.
This guidance should be followed to help avoid problems.
Guidance
Loading and unloading areas should be:
- Clear of other traffic, pedestrians and people not involved in loading or unloading.
- Clear of overhead electric cables so there is no chance touching them, or of electricity jumping to 'earth' through machinery, loads or people.
- Level. To maintain stability, trailers should be parked on firm level ground,
- Loads should be spread as evenly as possible, during both loading and unloading. Uneven loads can make the vehicle or trailer unstable.
- Loads should be secured, or arranged so that they do not slide around. Racking may help stability.
- Safety equipment must be considered. Mechanical equipment and heavy moving loads are dangerous.
- Guards or skirting plates may be necessary if there is a risk of anything being caught in machinery (for example dock levellers or vehicle tail lifts). There may be other mechanical dangers and safety procedures to be considered.
- Ensure the vehicle or trailer has its brakes applied and all stabilisers are used. The vehicle should be as stable as possible.
- In some workplaces it may be possible to install a harness system to protect people working at height. Provide a safe place where drivers can wait if they are not involved. Drivers should not remain in their cabs if this can be avoided. No-one should be in the loading/unloading area if they are not needed.
- Vehicles must never be overloaded. Overloaded vehicles can become unstable, difficult to steer or be less able to brake.
- Always check the floor or deck of the loading area before loading to make sure it is safe. Look out for debris, broken boarding, etc.
- Loading should allow for safe unloading.
- Loads must be suitably packaged. When pallets are used, the driver needs to check that:
- They are in good condition
- Loads are properly secured to them.
- Loads are safe on the vehicle. They may need to be securely attached to make sure they cannot fall off.
- Tail gates and sideboards must be closed when possible. If over-hang cannot be avoided, it must be kept to a minimum. The over-hanging part of the load must be clearly marked.
- If more than one company is involved, they should agree in advance how loading and unloading will happen.
- For example, if visiting drivers unload their vehicles themselves, they must receive the necessary instructions, equipment and co-operation for safe unloading. Arrangements will need to be agreed in advance between the haulier and the recipient.
- Some goods are difficult to secure during transport. Hauliers and recipients will need to exchange information about loads in advance so that they can agree safe unloading procedures.
Checks must be made before unloading to make sure loads have not shifted during transit, and are not likely to move or fall when restraints are removed.
There must be safeguards against drivers accidentally driving away too early. This does happen, and is extremely dangerous. Measures could include:
- Traffic lights.
- The use of vehicle or trailer restraints.
- The person in charge of loading or unloading could keep hold of the vehicle keys or paperwork until it is safe for the vehicle to be moved.
- These safeguards would be especially effective where there could be communication problems, for example where foreign drivers are involved.
Further information;
Control of substances hazardous to health (COSHH)
Using chemicals or other hazardous substances within warehouses can put people’s health at risk. The Control of Substances Hazardous to Health Regulations 2002 (COSHH) require employers to control exposure to hazardous substances to prevent ill health. Effects from hazardous substances can range from mild eye irritation to chronic lung disease or, on occasion, death.
Temperature at work
The temperature in warehouse operations should provide reasonable comfort without the need for special clothing. Typically, the temperature should be at least 16 °C. Where the work involves
severe physical effort, the temperature should be at least 13 °C. However, these temperatures may not ensure reasonable comfort.
Other factors, such as air movement and relative humidity, should also be considered. In warehouses, it may be impractical to maintain these temperatures because of specific storage temperature requirements, or because of the nature of the building (e.g. in buildings that have to be open to the outside). In these cases, take all reasonable steps to achieve a temperature that is as close as possible to a comfortable level.
Where a reasonably comfortable temperature cannot be achieved throughout your warehouse, provide local heating or cooling (as appropriate).
There are no specific upper temperature limits. However, the requirement for temperatures in the workplace to be reasonable applies. In extremely hot weather, fans and increased ventilation may be used instead of local cooling.
Where workers are exposed to temperatures that do not give reasonable comfort, provide suitable protective clothing and rest facilities. The provision of protective clothing should be considered as a last resort. In parts of the workplace other than workrooms, such as sanitary facilities or rest facilities, the temperature should be reasonable. Changing rooms and shower rooms should not be cold.
For more information see:
- The Approved Code of Practice on the Workplace (Health, Safety and Welfare) Regulations
- HSE Temperature
- ACAS working in extreme temperatures
Managing asbestos
The duty to manage asbestos is directed at those who manage non-domestic premises: the people with responsibility for protecting others who work in such premises, or use them in other ways, from the risks to ill health that exposure to asbestos causes.
Duty holders must:
- take reasonable steps to find out if there are materials containing asbestos in non-domestic premises, and if so, its amount, where it is and what condition it is in
- presume materials contain asbestos unless there is strong evidence that they do not
- make, and keep up-to-date, a record of the location and condition of the asbestos- containing materials - or materials which are presumed to contain asbestos
- assess the risk of anyone being exposed to fibres from the materials identified
- prepare a plan that sets out in detail how the risks from these materials will be managed
- take the necessary steps to put the plan into action
- periodically review and monitor the plan and the arrangements to act on it so that the plan remains relevant and up-to-date
- provide information on the location and condition of the materials to anyone who is liable to work on or disturb them
For further information see:
HSE - Managing Asbestos
Fire safety
You will also need to ensure that you have suitable fire precautions in place;
Fire safety precautions are enforced by Lancashire Fire and Rescue and not the Council.
Further information
National Fork Lift Safety Day
Last updated: 16 August 2024