Electrical safety
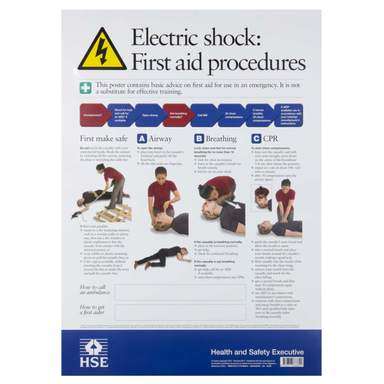
Electric Shock Poster - HSE
Electricity can kill or severely injure people and cause damage to property. However, employers can take simple precautions when working with or near electricity and electrical equipment to significantly reduce the risk of injury to you, your workers and others around you.
Even non-fatal shocks can cause severe and permanent injury. For example, shocks from faulty equipment may lead to falls from ladders, scaffolds or other work platforms. Those using or working with electricity may not be the only ones at risk – poor electrical installations and faulty electrical appliances can lead to fire, which may also cause death or injury to others. Most of these accidents can be avoided by careful planning and straightforward precautions.
The main electrical hazards
The main hazards of working with electricity are:
- electric shock and burns from contact with live parts
- injury from exposure to arcing (when electricity jumps from one circuit to another)
- fire from faulty electrical equipment or installations
- explosion caused by unsuitable electrical apparatus
- static electricity igniting flammable vapours or dusts, for example in a spray-paint booth
- Electric shocks can also lead to other types of injury, for example by causing a fall when working from ladders or scaffolds etc..
Even incorrectly wiring a plug can be dangerous and lead to fatal accidents or fires!
Actions you must take
You must ensure an assessment has been made of any electrical hazards, which covers:
- who could be harmed by them
- how the level of risk has been established
- the precautions taken to control that risk
The risk assessment should take into consideration the type of electrical equipment used, the way in which it is used and the environment it is used in.
You must make sure that the electrical installation and the electrical equipment are:
- suitable for their intended use and the conditions in which they are operated
- only used for their intended purpose
In wet surroundings, unsuitable equipment can become live and make its surroundings live too. Fuses, circuit-breakers and other devices must be correctly rated for the circuit they protect. Isolators and fuse-box cases should be kept closed and, if possible, locked.
Cables, plugs, sockets and fittings must be robust enough and adequately protected for the working environment. Ensure that machinery has an accessible switch or isolator to cut off the power quickly in an emergency
Fixed installations (the wires, circuits, consumer units, sockets, etc. of the building)
Electrical installations will deteriorate over time. The rate of deterioration will depend upon the frequency of use, the working environment and the maintenance schedule. To ensure the safety of your employees and customers it is important to test your electrical installations at appropriate intervals as part of a preventative maintenance programme. Not only does it protect people from danger, it also safeguards your organisation when it comes to the insurance of the site by demonstrating compliance with relevant workplace regulations
You should arrange for testing within the time period specified by the competent person (Usually an electrician) during the last inspection. This should cover circuits from the meter and consumer unit supplying:
- light switches
- sockets
- wired-in equipment (e.g. cookers, hair-dryers)
The work should normally be carried out by a competent person, usually an electrician.
Electrical Installation Condition Reports (EICR)
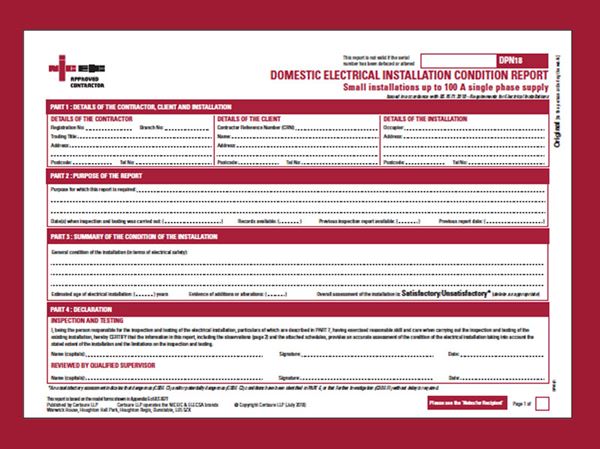
Inspection and testing by a qualified contractor will establish if an installation is safe for users. You will receive a copy of the Electrical Installation Condition Report (EICR) produced from the testing which will inform you about the overall condition of the electrics. Any faults are coded based on the risk of danger associated with them.
The EICR will show whether the electrical installation is in a 'satisfactory' or 'unsatisfactory' condition and will detail a list of observations affecting the safety or requiring improvements.
Unsatisfactory Codes are:
- C1 – Danger present, risk of injury, immediate remedial action required
- C2 – Potentially Dangerous, urgent remedial action required
- FI – Further investigation required
A Satisfactory Code is:
- C3 – Improvement recommended
Health and Safety Inspectors will ask to see inspection certificates and evidence that dangerous or potentially dangerous matters situations have been made safe (repaired or replaced).
Frequency of Inspection
5 Year Fixed Wire Testing
Most standard workplace environments need an Electrical Installation Condition Report to be produced at least every 5 years. However, there should be regular routine inspections conducted at least annually.
Typical workplaces which require 5 Yearly Fixed Wire Testing include:
- Commercial spaces such as offices and retail outlets
- Hotels and restaurants (excluding spa hotels)
- Schools, colleges and universities
- Laboratories
- Community centres, churches and public houses
- Care homes and hospitals (excluding medical locations)
- Halls of residence, houses of multiple occupancy
3 Year or 1 Year Fixed Wire Testing
Environments which, for example, are exposed to moisture, dust, extreme temperatures or which are open to the general public constitute a higher risk and therefore require more frequent testing. These workplaces require testing every 1 -3 years, with more frequent routine inspections also required.
Typical workplaces or environments which require 3 or 1 year Fixed Wire Testing include:
- Spa hotels and leisure centres – 3 years
- Industrial Units – 3 years
- Theatres and places of public entertainment – 3 years
- Caravans – 3 years
- Cinemas – 3 years (back of house), 1 year (front of house)
- Agricultural or horticultural establishments – 3 years
- Medical locations in hospitals or clinics – 1 year
- Swimming pools and saunas – 1 year
- Caravan Parks and Marinas – 1 year
- Fish Farms, Laundrettes, Petrol Stations – 1 year
Business with areas falling into more than one category
For example a hotel (5 years) with a swimming pool (1 year), or a manufacturing plant (3 years) with offices (5 years), or a leisure centre (3 years) with sauna (1 year). Each area will need to be inspected accordingly, so the electrician will come back every year to test the pool and sauna but only test the main hotel area every 5 years. It is also acceptable to break large premises down into areas and test a different area every year, so that the whole premises is inspected on a rolling basis.
Portable Appliance Testing (PAT)
Portable appliance testing (PAT) is the term used to describe the examination of electrical appliances and equipment to ensure they are safe to use. Most electrical safety defects can be found by visual examination but some types of defect can only be found by testing. However, it is essential to understand that visual examination is an essential part of the process because some types of electrical safety defect can't be detected by testing alone.
A relatively brief user check (based upon simple training and perhaps assisted by the use of a brief checklist) can be a very useful part of any electrical maintenance regime. However, more formal visual inspection and testing by a competent person may also be required at appropriate intervals, depending upon the type of equipment and the environment in which it is used.
Frequency of Inspection
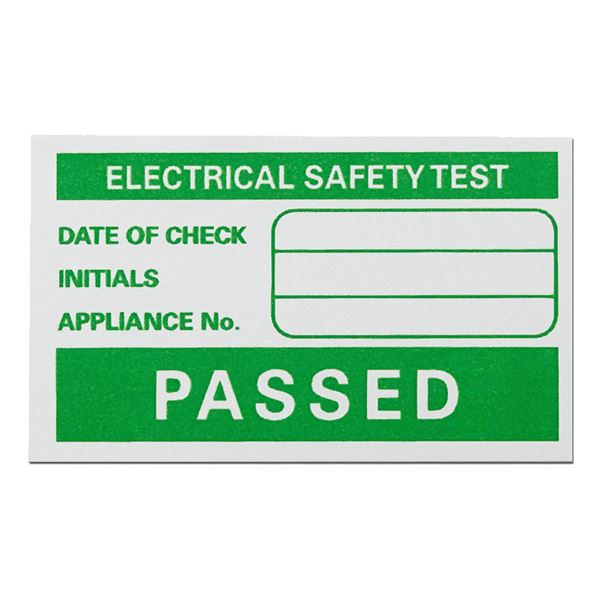
The frequency of inspection and testing depends upon the type of equipment and the environment it is used in. For example, a power tool used on a construction site should be examined more frequently than a lamp in a hotel bedroom.
For guidance on suggested frequencies of inspection and testing;
- Maintaining portable and transportable electrical equipment.
- Maintaining portable electrical equipment in low-risk environments
The table below gives a list of suggested initial inspection intervals for different types of equipment. The combined inspection and test could be a Portable Appliance Test (PAT), or a detailed test with a more sophisticated instrument. You should make sure that the person carrying out the tests is trained and competent to do so.
Type of business | User checks | Formal visual inspection | Combined inspection and test |
---|---|---|---|
Equipment hire | N/A | Before issue/after return | Before issue |
Construction (see Electrical safety on construction sites for more detail) | 110 V - Weekly 230 V mains - Daily/every shift | 110 V - Monthly 230 V - weekly | 110 V - Before first use on site then 3 monthly 230 V mains - Before first use on site then monthly |
Light industrial | Yes | Before initial use, then 6 monthly | 6 months to 1 year |
Heavy industrial/high risk of equipment damage | Daily | Weekly | 6 months to 1 year |
Office information technology e.g. desktop computers, photocopiers, fax machines | No | 1 to 2 years | None if double-insulated, otherwise up to 5 years |
Double insulated equipment not hand-held, e.g. fans,table lamps | No | 2 to 3 years | No |
Hand-held double insulated (Class II) equipment, e.g. some floor cleaners, kitchen equipment and irons | Yes | 6 months to 1 year | No |
Earthed (Class I) equipment, e.g. electric kettles, some floor cleaners | Yes | 6 months to 1 year | 1 to 2 years |
Equipment used by the public, e.g. in hotels | By member of staff | 3 months | 1 year |
Cables and plugs, extension leads | Yes | 1 year | 2 years |
Electrical Overloading
An electric overload occurs when too much current passes through electric wires. The wires heat and can melt, with the risk of starting a fire. The solution? Avoid plugging several power-hungry items of equipment into the same line. This is a common problem in many commercial kitchens. Most commercial equipment should be plugged into a socket which is wired into the ring main and not into an extension cable.
This on-line socket over-load calculator shows how easy it is to overload your electrical circuit.
Residual Current Device's (RCD)
A Residual Current Device (RCD) can reduce the likelihood of an electrical injury but a shock can still cause very serious or fatal injuries, so an RCD should only be used as a secondary means of reducing the risk of people being injured by electricity. An RCD detects some, but not all, faults in the electrical system and rapidly switches off the supply, reducing the potential for injury caused by a common type of electric shock
The best place for an RCD is built into the main switchboard, as this means that the electrical supply is permanently protected. If this is not possible, an electrical socket outlet incorporating an RCD, or a plug in RCD adaptor, can also provide additional safety.
If an electrical socket outlet incorporating an RCD, or a plug in RCD adaptor is used it should be tested, by the user, prior to use by operating the Test button. Faulty RCDs should not be used and either removed for use or labelled as faulty.
Competent person (e.g.. Electricians)
People working on electrical equipment, machinery or installations must be competent to do so. The level of competence required to do a task is dependent upon the complexity of that task and the amount of knowledge required. Assessing the suitability of an individual to do a task requires evidence of:
- Training to an appropriate level in the area of work
- Experience of achieving a suitable standard in similar work.
- Regular re-assessment.
People who cannot demonstrate competence should not be allowed to work unless they are supervised by someone who is.
The Memorandum of guidance on the Electricity at Work Regulations 1989 provides information on competence.
You can search for a competent person at the following organisations:
More information
- Electrical safety and you: A brief guide
- Maintaining portable and transportable electrical equipment.
- Maintaining portable electrical equipment in low-risk environments
- Electricity at work Safe working practices
- Electrical safety for entertainers
- Maintenance priorities in catering
- Using electric storage batteries safely
- The Electricity at Work Regulations 1989: Guidance on Regulations
Last updated: 16 February 2024