Childcare & Nurseries
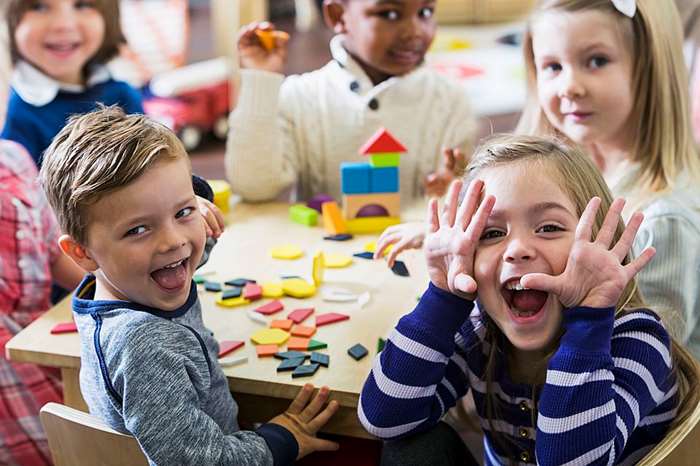
Children
This page provides guidance for people and organisations that look after children such as childminders and nurseries.
Ten safety essentials
Take a look at our ten safety essentials pages. These pages will guide you through the essentials for managing health and safety in your business. The areas below contain specialist advice for you to consider when writing your risk assessments and implementing safe systems of work & procedures to keep staff and visitors safe.
Risk assessment
When undertaking your risk assessment for your business you may wish to look at these examples to give you ideas of hazards and control measures:
Example Risk Assessment for Nurseries and Childcare (PDF, 729KB)
You may also wish to consider the other topics which may be relevant to parts of your premises:
- Food preparation, cooking and service
- Office based business
Emergancy Planning
You should also ensure that you have adequate plans in place for emergencies. See the GOV UK Emergency planning and response for education, childcare, and children’s social care settings pages.
Choking risks
Choking occurs when a foreign object becomes stuck in the airway and prevents breathing. Young children are particularly vulnerable because their trachea and bronchi which carry oxygen to the lungs are small and they have not yet developed full control of the muscles in their mouth and throat. Items of food or other objects put into the mouth can therefore easily become trapped.
In most cases, the item can be dislodged by coughing. However, sometimes this does not work and without immediate first aid the incident can quickly become life-threatening.
Risks may be greater for under-threes who often explore the world around them by putting things in their mouths. Older children can be taught about the dangers of such behaviour, but will still be at risk, particularly from food.
People of any age can choke while they are eating or drinking. However, children are more at risk than an adult because they do not chew as well, their swallowing may not be as co-ordinated and they get distracted during mealtimes.
In all cases, an early years service must complete appropriate risk assessments. Robust assessments should inform suitable policies and procedures designed to reduce risks to a minimum and to support contingency plans in case of an incident.
Risk assessments should be completed by a competent person and should be subject to regular review.
Further reading
Making up and heating drinks such as milk
Scalds
Heating milk in bottles or cups should be undertaken using a bottle warmer. Milk and other drinks must not be heated in the microwave or on a stove. Microwaves heat the milk unevenly, causing hot spots that can scald a child's mouth. Heating milk in pans/jugs of boiling water should also be discouraged due to the risk of scalding if busy staffknock the jug over themselves. If you wish to warm milk for a toddler, place a bottle of milk into the bottle warmer, then transfer the warm milk into the appropriate cup/beaker. Once milk has been heated, it should be temperature checked prior to being given to a child, it is acceptable to check the temperature of milk on the inside of your wrist, the milk should feel warm not hot. You should include heating milk into your risk assessments and ensure you produce and implement a safe system of work for staff to follow, many premises often produce a bottle/milk warming policy that includes step by step instructions for their staff to follow.
Food Safety
Follow the NHS guidance on making up baby formula safely.
Play equipment
Health and safety laws and regulations are sometimes presented as a reason why certain play and leisure activities undertaken by children and young people should be discouraged. Such decisions are often based on misunderstandings about what the law requires. The HSE has worked with the Play Safety Forum to produce a joint high-level statement that gives clear messages tackling these misunderstandings. HSE fully endorses the principles in this Statement.
This statement makes clear that:
- Play is important for children's well-being and development
- When planning and providing play opportunities, the goal is not to eliminate risk, but to weigh up the risks and benefits
- Those providing play opportunities should focus on controlling the real risks, while securing or increasing the benefits – not on the paperwork
- Accidents and mistakes happen during play – but fear of litigation and prosecution has been blown out of proportion
Children's Play and Leisure: promoting a balanced approach (PDF)
RoSPA Guidance on play equipment: Play Safety
Musculoskeletal disorders
What you must do
The Manual Handling Operations Regulations 1992 (MHOR) require employers to:
- avoid the need for hazardous manual handling, so far as is reasonably practicable;
- assess the risk of injury from any hazardous manual handling that can't be avoided; and
- reduce the risk of injury from hazardous manual handling, so far as is reasonably practicable.
Your risk assessment should cover all standard operations, including cleaning and maintenance activities. It should reflect how the work is actually done.
The main areas you should focus on are the task, load, working environment and individual capability.
Using cots
Employers should make sure workplaces use cots which minimise the distance employees need to bend and reach.
- Cots should be of a height that will enable employees to lift and lower children into and out of the cots with minimal forward bending of the employee's back.
- If cots have two base positions, set the base to the higher position for infants unable to stand. The higher base position will reduce the need for employees to reach into cots.
- Cots should have sides that drop to reduce the need for employees to bend and reach over the cot side to lift and lower children. At its dropped level, the top of the cot's lowered side should be at least 250mm above the top of the mattress to ensure children cannot roll out of the cot.
- Ensure there is enough clearance under cots for employees to stand with their feet under the edge of the cot to minimise reaching distance.
- Prepare cots in advance so sides are down before employees lift children in or out.
- If cots have wheels, ensure the wheels have locks and keep wheels in the locked position when the cot is not being moved.
- Regularly check and maintain cot wheels, wheel locks and drop-down sides to ensure cots are safe and secure.
- Assess floor surfaces to ensure minimal friction and resistance when wheeling cots. Change floor surfaces so employees can easily move cots.
- Ensure cots meet all relevant structural safety requirements
Using highchairs
Employers should make sure workplaces use high-chairs which minimise bending, reaching and twisting when lowering or lifting children in the chairs.
- Use high-chairs with removable or adjustable trays so employees can lower or lift children before putting the tray in place.
- Use high-chairs which do not have obstructions at floor level so employees can stand with their feet under the edge of the seat to minimise reaching distances when lifting children into or out of the chair.
- Use high-chairs of a height that allows employees to lift and lower children into and out of the chair with minimal forward bending of the employee's back.
- If high-chairs have wheels, ensure the wheels have locks and keep wheels in the locked position when the chair is not being moved.
- Assess floor surfaces to ensure minimal friction and resistance when wheeling high-chairs. Change floor surfaces so employees can easily move high-chairs.
- Consider alternative feeding arrangements for children who are able.
Using change tables
Employers should make sure workplaces use change tables which minimise bending, reaching and twisting when employees are using change tables. The list below provides suggestions on how to reduce the risk of injury.
- Use change tables with steps so children who are able can walk up and down to the change table surface, removing the need for employees to lift children. The step size and number of steps should be suitable for the smallest child using the change table.
- Moveable and portable steps should be made from lightweight and strong materials.
- Use change tables with a handrail to aid the child to climb the steps.
- Use change table steps that protect the child from a fall from an unprotected edge.
- Children should be prevented from accessing the steps unsupervised or when the steps are not in use.
- Use change tables with space underneath for employees' feet so they can stand close to the child being changed.
- Use height-adjustable change tables so employees can adjust tables to waist height.
- Make sure employees have sufficient access around the change table so they can change the child from a front position with the child's feet facing the employee's stomach.
- Make sure changing supplies and waste disposal facilities are within easy reach, reducing the need for employees to repeatedly twist, bend or use an extended reach.
- Avoid change tables that require children to be left unrestrained or require the employee to use force, bend, twist or reach when assisting children onto and off the change table.
Find out more
- MSD microsite
- Manual handling assessment (MAC) TOOL
This helps user identify high risk workplace manual handling activities - Are you making the best use of lifting and handling aids
- Manual handling at work: A brief guide
- Manual handling assessment charts
- Upper Limb Disorders in the Workplace
- Aching Arms (or RSI) in small businesses
Control of substances hazardous to health (COSHH), including infection control
The law requires you to adequately control exposure to materials in the workplace that cause ill health. This is the Control of Substances Hazardous to Health Regulations (COSHH).
Harmful substances
Many materials or substances used or created at work could harm your health. These substances could be dusts, gases or fumes that you breathe in, or liquids, gels or powders that come into contact with your eyes or skin. There could also be harmful micro-organisms present that can cause infection, an allergic reaction or are toxic.
Harmful substances can be present in anything from paints and cleaners to flour dust, solder fume, blood or waste. Ill health caused by these substances used at work is preventable. Many substances can harm health but, used properly, they almost never do.
Safety data sheets
Manufacturers ans suppliers of chemicals have a duty to provide safety data sheets to consumers. You should acquire the safety data-sheets for the chemicals you use in your business and use them as the basis for your COSHH risk assessments. You can contact suppliers directly or often find the data-sheets on-line.
Infection Control
- Preventing and controlling infections
- Managing outbreaks and incidents
- Infectious diseases: exclusion table
- Cleaning up body fluids
Training: Preventing and Managing Infections in Childcare and Pre-school
Further information
- HSE website COSHH
- How to carry out a COSHH risk assessment
- A brief guide to COSHH (INDG136)
- COSHH Essentials
- Safety data sheets - Virtual college safety data-sheets & COSHH
Key considerations
- All paints and glue used for children’s activities must not be openly available to use (keep locked away).
- When the children are using paints and glue they must be supervised at all times.
- All cleaning products to be kept in a locked cupboard not accessible to the children, including frequently used sanitising sprays.
- Remember even 'household' chemicals such as bleach & sanitizers (including sanitising wet wipes) can quickly cause harm, all chemicals should be removed from surfaces prior to allowing children to use/touch them.
- All cleaning products are to be labelled and in their original containers.
- Disposable (latex free) gloves are to be used when cleaning bodily fluids
- Should a child ingest a hazardous product first aid must be administered seek medical help, ensure a COSHH data sheet is to hand to take to hospital & show the doctors, if necessary.
Reporting children's accidents and injuries
When a member of the public (a child) is taken from a workplace (e.g. the nursery) directly to hospital, whether in an ambulance, car, taxi or other, then that must be reported under the RIDDOR regulations to us.
You also have a duty to report certain injuries and illness to Ofstead: Childcare: reporting children’s accidents and injuries
Gas safety
Many premises use gas for cooking and heating. It is essential that all business know and understand their duties in relation to gas safety. In order to comply with the law, as a business you should;
- Have your gas installation (the building including pipe work) inspected by a gas safe engineer, and; (This is usually an annual inspection)
- Have your gas appliances (cookers, grills, heaters, boilers etc...) inspected by a gas safe engineer; (This is usually an annual inspection)
- Keep all records of inspection for at least two years, to demonstrate that you are having the checks undertaken
See our Gas safety page for comprehensive guidance.
Top tips for using gas heaters in gazebo's, marquees & other shelters.
- Gas appliances such as heaters or lamps must be suitable for ‘indoor use’. Gas equipment such as patio heaters are frequently only rated for ‘outdoor use’, due to the dangerously high mounts of Carbon Monoxide they emit. Consult the instruction manual for your gas appliance prior to operation. If you cannot find the instruction manual consult with a competent Gas Safe Engineer.
- Ensure all staff are trained in the changing and operation of gas cylinders.
- Spare gas cylinders (full and empty) must be stored outside in a locked cage. The cage must not be located near to drain or cellar access.
- Persons, especially children, must be protected from burns brought about from being too close to or touching hot patio heaters.
Electrical safety
Electricity can kill or severely injure people and cause damage to property. However, employers can take simple precautions when working with or near electricity and electrical equipment to significantly reduce the risk of injury to you, your workers and others around you. There have been a number of high profile deaths in hospitality premises in recent years, therefore you must:
- Ensure the electrical installation is inspected and maintained in good repair; and
- Ensure that any portable appliances are inspected and tested regularly (PAT Test);
- Keep a records of inspections and tests.
See our Electrical safety page for comprehensive guidance.
Managing asbestos
The duty to manage asbestos is directed at those who manage non-domestic premises: the people with responsibility for protecting others who work in such premises, or use them in other ways, from the risks to ill health that exposure to asbestos causes.
Duty holders must:
- take reasonable steps to find out if there are materials containing asbestos in non-domestic premises, and if so, its amount, where it is and what condition it is in
- presume materials contain asbestos unless there is strong evidence that they do not
- make, and keep up-to-date, a record of the location and condition of the asbestos- containing materials - or materials which are presumed to contain asbestos
- assess the risk of anyone being exposed to fibres from the materials identified
- prepare a plan that sets out in detail how the risks from these materials will be managed
- take the necessary steps to put the plan into action
- periodically review and monitor the plan and the arrangements to act on it so that the plan remains relevant and up-to-date
- provide information on the location and condition of the materials to anyone who is liable to work on or disturb them
Further information:
HSE - Managing Asbestos
Fire safety
You will also need to ensure that you have suitable fire precautions in place;
- A guide to making your small non-domestic premises safe from fire
- Small and medium places of assembly
- Large places of assembly
Fire safety precautions are enforced by Lancashire Fire and Rescue and not the Council.
Further resources
Last updated: 01 October 2024